Abhishek Bana
Green Entrepreneur
India As Global Solar Manufacturing Hub Post COVID19
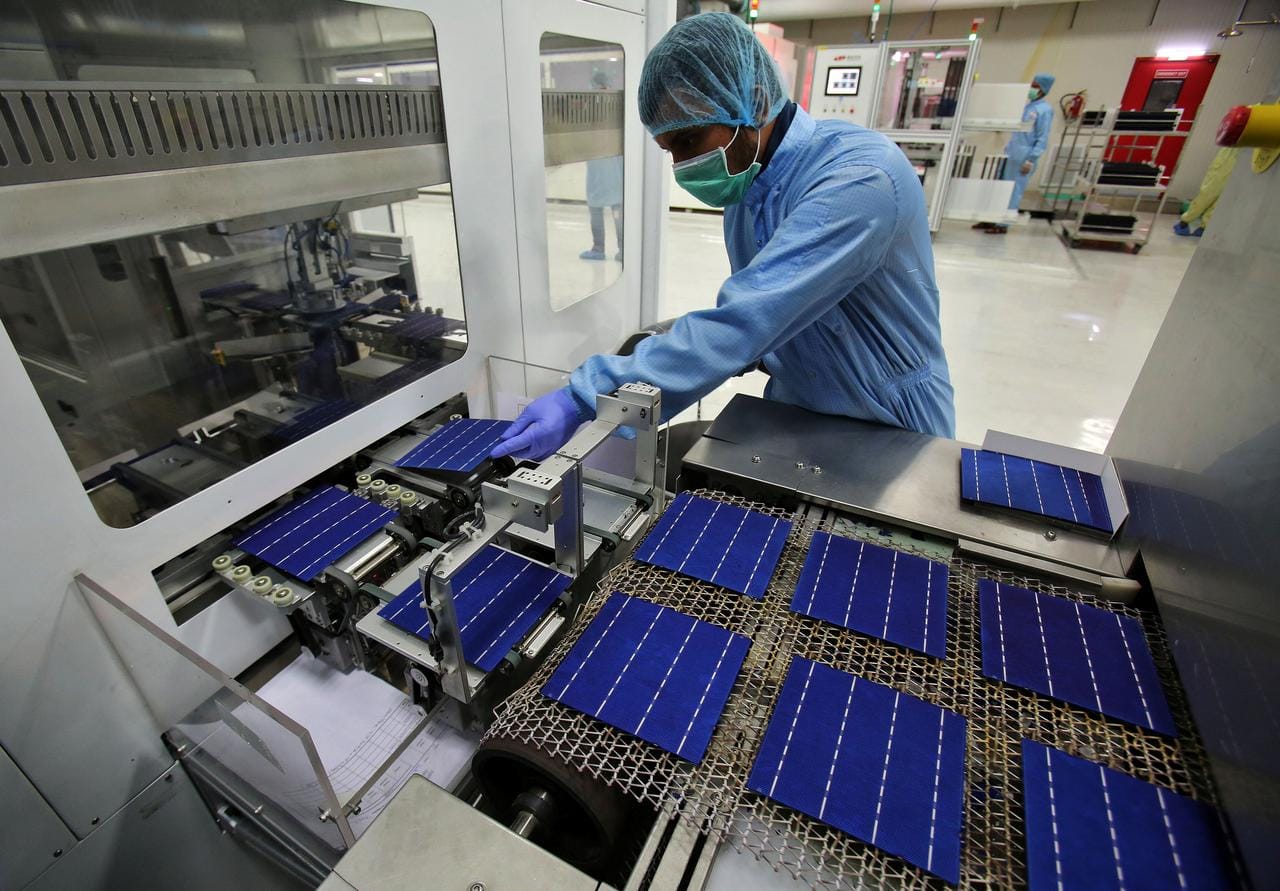
Can India be an international hub for solar manufacturing? The answer is a big capital YES. As usual, an accurate answer needs much more analysis, prediction and explanation. In this article, we shall discuss the global scenarios which may positively push India to become the world leader in solar manufacturing. Of course, the push must be well accepted by our country with the help of domestic solar players and policy makers by modifying our current approach to the manufacturing industry.
Challenges and Solutions
In the pre COVID-19 world, there were multiple problems or shortcomings in the Indian solar industry which will continue to persist in the post COVID-19 world as well. It is wise to address them first. Overcoming these issues will make the industry much more sustainable. After all, we are in it for a sustainable, long term manufacturing hub.
Lack of Special Focus
The Indian government has paid attention to many fields such as the automobile and food processing industry. A reduction in the Goods and Services Tax rate to 18 percent on vehicles and introduction of an incentive-based scrappage policy is a very welcome step for the automobile industry. Food processing industry enjoys income tax exemptions under Section 35AD of the Income Tax Act. Such special allowance and focus has helped automobile and food processing industries to penetrate and grow into the competitive global market. The Solar Industry, at this point of time lacks such special focus from the government.
Inaccurate Demand Forecasting
Current manufacturers can not forecast the future solar demands owing to the uncertain nature of the domestic projects. Most of the inland projects are not executed within expected time, leading to inaccurate market demand forecasting. Hence the existing manufacturing units are working at an average of 60% of their full production capacity. To fix this problem, the current players (manufacturers & EPC contractors) are supposed to make realistic estimation and try to complete the projects without exceeding the buffer time. At the same time, local regulatory bodies such as DISCOMS should fastrack the paperwork of any solar project. Increased utilisation of the existing capacity will attract more domestic and international investors. Perhaps, a single window approach serves well in this case. This will tremendously improve demand forecasting in the country.
Complex Taxation and Legal structure for FDI
Foreign Direct Investments are like the boosters for a rocket to take off from the ground. Although the industry can completely thrive on domestic investments, a surge in foreign funds will kick start the solar industry at high acceleration. Solar industry in India lacks a streamlined, simple FDI structure. Hence, foreign investors shy away from investing in this industry. A large share of total FDI goes into automobile(10%), service (32%), telecommunication(15%) and infrastructure (9%) industry. Power industry only received 3.6% of the total FDI in FY2019. Out of that only 30% headed to the solar industry. Easing taxation policies and opening a single window especially for Solar FDI will boost the industry greatly. Industry wise FDI cash inflow for the financial year 2019 is shown in the charts below.


Certifications
Standard Certification brings reliability, quality and efficiency in the products. Certifications are necessary to develop a sustainable industry in a country or globally. Small manufacturing units usually do not have the capital to invest in the certifications with high prices. Besides, banks do not consider certification as capital investment. Hence most of the small and medium scale manufacturers are unable to cater to the larger audience who demand quality certifications.
The investment in certifications needs to be subsidised by the government and globally accepted standards such as IEC must be accepted for large scale and small scale public projects. Recently, Indian government introduced BIS Certification of solar modules and other products which does not add any value to the existing global standard such as IEC. Manufacturers who have already invested in IEC certification must simply shell out money to get BIS tests done for certification which is technically the same as the IEC test certification.
Indigenisation of Complete Value Chain
Solar cells and modules alone do not make up the entire solar power system. There are a lot of other essential equipment to harness solar energy and utilise it. Indian manufacturers and local regulatory bodies should focus on manufacturing products such as inverters, high quality mounting structures, tracking devices etc. within the country. This will develop the industry as a whole.
Lack of Regional Solar Manufacturing Hubs
Although there are multiple solar manufacturing and services companies, they are widely dispersed in the entire country. This makes logistics a huge problem. The raw material suppliers are further away from manufacturers thus increasing the manufacturing cost. Regionally centralised manufacturing hub with a research center, raw material suppliers alongside and finished goods storage cells all over the country makes a better model that could cater a country as big as India.
Focus on latest technology, Research and Development
In India, there is no special advantage or subsidy given for manufacturing and supplying latest and emerging technology based solar products. Thus most of the manufacturers stick to the less expensive and widely accepted products. This hinders the progress of the country in terms of innovation. Governments should subsidise the use of the latest technology and promote manufacturing of state of the art solar products. Chinese government started promoting solar mono crystalline cells and module production in 2018. Mono crystalline panels are much more efficient than the polycrystalline. By the end of 2019, 80% of the modules manufactured in China were monocrystalline. This brought down the price of monocrystalline systems and thus making it a wise choice in the current days. Such steps should be taken by the Indian government too. Private investors and project developers should insist on using the latest technology which creates a healthy demand in the market. This inturn creates a space for research and development and indirectly allows Indian manufacturers to compete in the global market.
These are the shortcomings of Indian domestic manufacturing that are prevailing since 2015. With a concrete plan by the policy makers and close cooperation of the industry leaders, these can be overcome.
Post COVID19 Analysis and Projections
It is evident that most of the industries are affected by the COVID-19 pandemic. Excluding a few industries such as pharmaceuticals, healthcare and the food industry, rest have been affected to a great extent. According to MERCOM there are multiple effects of COVID-19 that are already being observed in the solar industry such as delayed PPA billing and payment, reduction in solar investment by 31% in Q1 of 2020. Other than that, there are multiple job losses, shutdown of small scale manufacturers and delayed commissioning of new solar manufacturing units and power plants.
Just like the two sides of a coin, COVID-19 also has some positive effects on the solar industry. These positives can be amplified with certain specific modifications to our current industry.
Low Oil Prices
The COVID-19 crisis has reduced the crude oil prices as low as USD 20 per barrel in mid April 2020. It is evident that the Government of India heavily subsidised oil prices. Since the international prices are low, these subsidies can be safely and economically shifted to the solar industry. Lower prices means faster ROI (Return on Investment), ergo creates demand. Hence the manufacturing plants in the country can grow at a higher pace.
Reduction in PV Prices
China, Germany, Japan and a few other countries have already reduced the PV and other raw material prices due to the global decrease in demand. Indian solar industry can take advantage of this price fall and start producing products on a large scale.
Monocrystalline Vs. Polycrystalline Price Gap
The price gap between the monocrystalline and polycrystalline cells is seen at 25% currently and is projected to drop down to 10% by Q3 of 2020. Indian manufacturers can take advantage of this lower price gap and shift towards superior and more efficient technology.
Post COVID19 Geopolitics
Industry analysts have presented a strong case for competitive non-chinese manufacturing to meet global demand. Owing to the huge manpower that is at disposal in India, manufacturers can use it to meet the global solar demands. Thus increasing the overall production capacity and incorporating latest technology. Quick expansion in the manufacturing will also bring down the price, making India a competitive alternative to China.
Conclusion
Every tunnel has a ray of light in the end. Just like that Indian solar manufacturing is capable of growing at a healthy rate with suggested changes in the industry. When the world emerges from the disruption of COVID-19, the imperative lies with the government and other major solar players. There are costs to be paid but that also offers a narrow window of opportunity. A strong response by the policy makers will go a long way in cashing on the opportunity by domestic solar manufacturers.
References
- http://incometaxmanagement.com/Pages/Tax-Ready-Reckoner/GTI/Business-Profession/Deduction-for-expenditure-on-setting-up-Specified-Business-Sec-35AD.html
- https://www.thehindubusinessline.com/economy/budget-expectations-lower-gst-incentive-based-scrappage-policy-tops-the-auto-sectors-wish-list/article30674594.ece
- https://mercomindia.com/mercom-coronavirus-live-updates-clean-energy-india/
- https://www.statista.com/statistics/711398/india-fdi-equity-inflows-distribution-by-sector/
Very apt. Right time to focus on solar energy.